产品描述
本机组主要用于将Φ8mm的铜杆拉制成Φ1.20-Φ4.0mm的铜丝,并在拉丝后直接连续进行退火软化,然后由Φ630/Φ500双盘收线机或Φ650型圈式收线机收线,生产的产品符合GB3953要求。
1. 设备主要性能
1.1 进线直径 Φ8mm
1.2 出线直径 Φ1.20-Φ4.0mm
1.3 拉丝模数量 13个
1.4 拉丝轮直径 Φ450mm
1.5 出线速度 25m/s
1.6 收线电机 2×22kw(DC)
1.7 退火方式 直流退火
1.8 主电机 280kw(DC)
1.9 定速轮电机 90kw(DC)
1.10 圈式收线电机 22kw
1.11 退火 功率 360KVA
2. 设备组成
2.1 放线架 1台
2.2 拉线主机 1台
2.3 卧式退火装置 1台
2.4 储线张力控制装置 1套
2.5 Φ630/Φ500双盘收线机 1台
2.6 Φ650型圈式收线机 1台
2.7 轧头穿模机 1台
2.8 电气控制系统 1套
2.9 蒸汽发生器 1套
2、10齿轮箱润滑系统 1套
3. 各部件规格特性要求
3.1 放线架
3.1.1 立柱式放线架,横臂可以转动,下面可放二盘圈线。
3.1.2 附全线连动停车装置。
3.1.3 放线高度 5m
3.2 拉线主机
3.2.1 进线直径 Φ8mm
3.2.2 出线直径 Φ1.20-Φ4.0mm
3.2.3 出线速度 25m/s
3.2.4 拉伸道数 13道
3.2.5 定速轮直径 Φ450mm
3.2.6 线模直径 Φ54×Φ38mm
3.2.7 出线模为回转模
3.2.8 每模穿线设点动开关:6只脚踩式,并设有防逆装置
3.2.9 主电机功率 280KW(DC)
3.2.10 定速轮及退火传动功率 90KW(DC)
3.2.11 齿轮箱润滑系统
使用4kwAC马达油泵、经油槽、热交换器、压力表油管,对各齿轮箱轴承进行润滑。
3.2.12 门盖:内外两层,采用不锈钢板,人工打开。正常开机情况下拉丝液不会溅出。
3.2.13 出口设断线检测装置
3.2.14 冷却润滑液供给系统:向各段拉丝模供给冷却润滑液,满则自动排入循环槽。
3.2.15 冷却润滑液槽与齿轮箱中间设有空间隔开,防止液体混入齿轮油中。
3.2.16 拉丝轮材质:表面喷涂碳化钨,保用1年。
3.2.17 齿轮采用高精度磨齿斜齿轮作为主传动齿轮。
3.2.18 带乳化液泵及换热器,热交换器为16m2。
3.3 退火装置
3.3.1 进线直径 Φ1.20-Φ4.0mm
3.3.2 退火线速 20m/s
3.3.3 退火方式 连续电阻式(二段)
3.3.4 退火 电流 6000A(DC)
3.3.5 退火 电压 60V(DC)
3.3.6 退火轮直径(名义直径) Φ420mm
3.3.7 退火铜轮包覆冷轧镍带
3.3.8 退火软化室使用蒸汽保护,设手动调压阀。
3.3.9 动力传动控制
动力由定速轮通过平皮带传动,联动控制,且可选择退火或不退火;用离合器切换控制,并设有防逆装置。
3.3.10 退火段
依次分为预热段、退火段、冷却段、个别退火段需有差动长度。各段导轮速度需考虑铜线之伸长量。
3.3.11 轴承润滑系统
润滑站的稀油对各轴承循环润滑。
3.3.12退火铜轮压缩空气冷却
3.3.13出口处设吹干装置
3、3、14退火冷却采用水循环冷却
3.4储线张力控制
3.4.1 适用线经 Φ1.20-Φ4.0mm
3.4.2 储线量 ≥5m
3.4.3 移动导轮直径 Φ270mm
3.4.4 固定导论直径 Φ350mm
3.4.5 导轮材质为LY111(铸铝),表面高温喷涂碳化钨。
3.4.6 张力控制: 张力控制采用气缸气压调节,连续可调且与收线同步可调。
3.4.7 断线检出: 断线自动停机
3.4.8 点动开关:点动踏板开关1只
3.5 Φ630/Φ500气电双盘收线机
Φ630/Φ500气电双盘收线装置是按德国尼霍夫 机型设计,其使用性能与进口设备相近。
3、5、1 排线直径范围 Φ1.20-Φ4.0mm
3、5、2 收线盘规格 PND500、PND560、PND630
3、5、3 收线 速度 20-25m/s
3、5、4气动蝶式刹车
3、5、5 定长自动切换盘,气压升降、气动夹紧、设机械保护
3、5、6 排线控制:独立电机1台,双排线杆。依线直径、线速大小自动排线。
3、5、7捕线器:捕线成功率不小于99%。
3、5、8 计米器:计米准确、精度高且有计米换盘功能。
3、6 Φ650型圈式收线机
3.6.1 收线速度 25m/s
3.6.2 收线架规格 Φ480×Φ860×1260mm
3.6.3 收线架载重量 1300kg
3.6.4 收线电机功率 22kw
3.6.5 排线电机功率 0.55kw
3.6.6 盘架移动电机功率 1.1kw
3.6.7 定长不停机换架
3.6.8 收线方式: 梅花下线
3.7 轧头穿模机
3.7.1 轧头滚轮直径 Φ110mm
3.7.2 进线直径 Φ1.2~Φ8.0mm(冷轧铜杆)
3.7.3 鼓轮直径 Φ430×300mm
3.7.4 鼓轮转速 16r/min
3.7.5 电机功率 5.5kw(DC)
3.8 电气系统
3.8.1 本机电源为三相五线制: 380V(±10%)50HZ
3.8.2 整机连动控制采用西门子PLC控制
3.8.3 电气控制箱
3.8.3.1 大拉线机主控制台(带人机触摸屏)
3.8.3.2 主机电源柜及传动柜
3.8.3.3 双盘收线机控制柜
3.8.3.4 圈式收线控制柜
3、8、3、5 退火控制柜
3、8、3、6 退火电源控制柜(包括变压器)
3、9 电气系统主要特点:
3、9、1 传动
整条生产线传动均采用直流电机拖动,采用西门子全数字直流控制器进行控制,由于控制采用了数字量测速机和数字量给定,调速精度可以达到0.006%,从而保证整条线的调速精度。
3、9、2 退火
退火采用直流退火,输出电流 可以达到6000A, 电压60V,控制采用数字式可控硅触发板和调节板,输出线性好,稳定性高,保证了铜线在退火后延伸率的稳定。
3、9、3 控制
直流传动由于采用全数字直流控制器,调速精度有保证;收线自动跟踪线速度,通过储线装置调整收线的速度,保证与主机的同步;同时退火跟随线速度自动调整输出电压,保证铜线在不同的线速度下的延伸率均能达到要求。
控制采用可编程控制器集中控制,操作采用大屏幕人机界面。
可编程控制器与各台直流控制器通过通讯连接,各段速度由可编程控制器进行计算后通过通讯传输给各台直流控制器,从而保证了拉线过程中各台电机的调速精度,采用通讯稳定性高、故障率低,由于控制精度高也保证了双盘收线在满盘换盘时的成功率。
操作通过大屏幕人机界面,全为中文指示,操作直观、简单,同时对设备的运行状态、故障均有指示,便于设备的检修和维护。
4. 机组主要特点
4.1 本机组按德国尼霍夫 机型M85设计,设备外形美观,结构 ,运行噪音小,生产效率高,经济效益高。
4.2 拉丝鼓轮采用一系列式倾斜排列结构,避免铜线擦伤挤压。机器强度高,钢性好。定速轮和拉丝轮由不同电机驱动,采用 的总线结构,且速度同步可调,可实现快速换模。
4.3 拉丝鼓轮为全浸没式冷却,拉线模及铜线可得到 冷却和润滑。
4.4 拉丝鼓轮、定速轮和导轮经喷碳化钨处理,硬度高,耐磨性好,使用寿命长。
4.5 高精度磨齿斜齿轮传动,设有欠油保护。
4.6 退火机采用卧式两段式连续直流退火结构特别适用于以废铜为原材料生产的低氧铜杆。软化程度充分、结构合理、操作方便。退火采用 的全数字控制板,控制精度高,稳定靠高,退火电流的数字化调节和退火电压的自动跟踪使得退火导线的生产质量稳定,优良。在开机、关机及连续运行时,导线的延伸率始终保持恒定,而且实现零长度退火(即整盘从头到尾无未退火线)。
4.7 拉丝主电机、定速轮驱动电机及收线电机均采用进口全数字直流调速装置,调速精度高。
4.8 双盘收线机采用 设计的气电相结合的结构,稳定性好,干净无漏油污染。特殊的结构设计保证线盘最里层在放线时不松线,节约了运行成本。
4、9 双盘收线自动换盘成功率达到99%以上。
4、10 电气系统采用PLC控制和触摸屏统一操作。工艺参数可在触摸屏中设定、修改、显示。各种运行参数集中控制、诊断。系统 、操作方便。
5、 随机辅助部件
5、1 蒸汽发生器
5、2 机油润滑供应站
产品图片
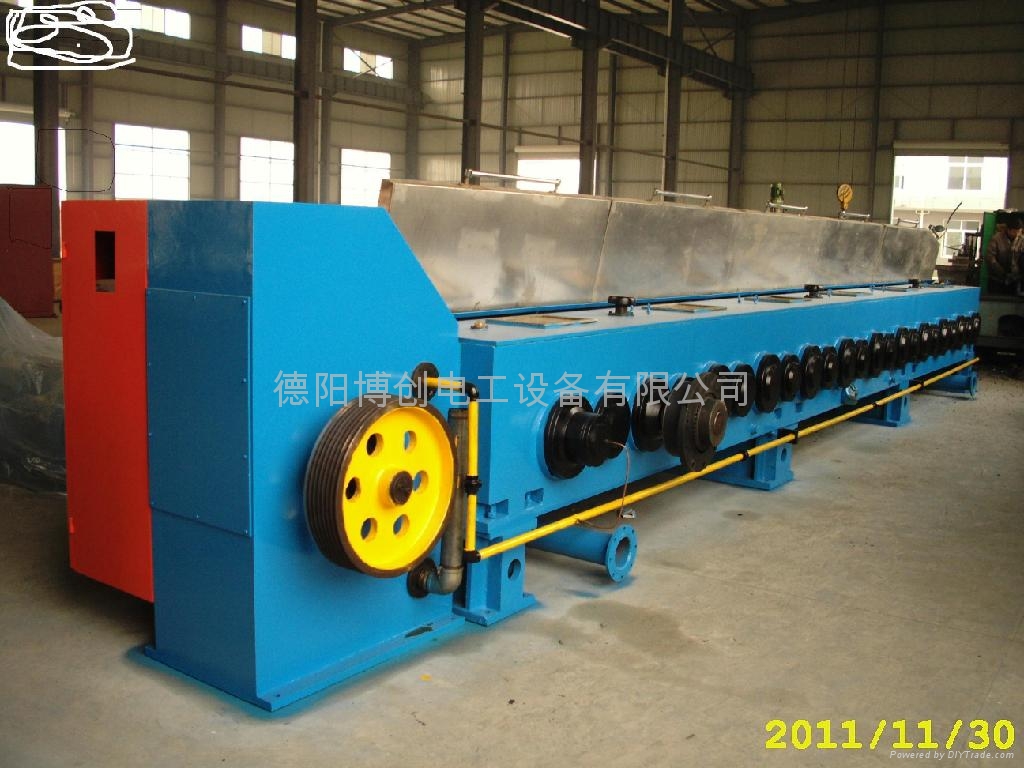
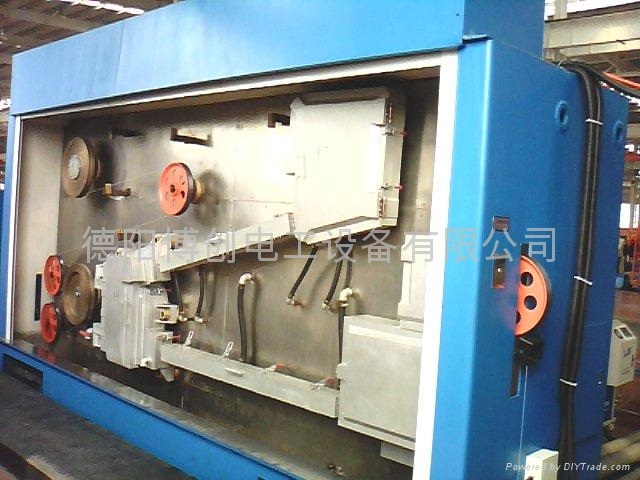
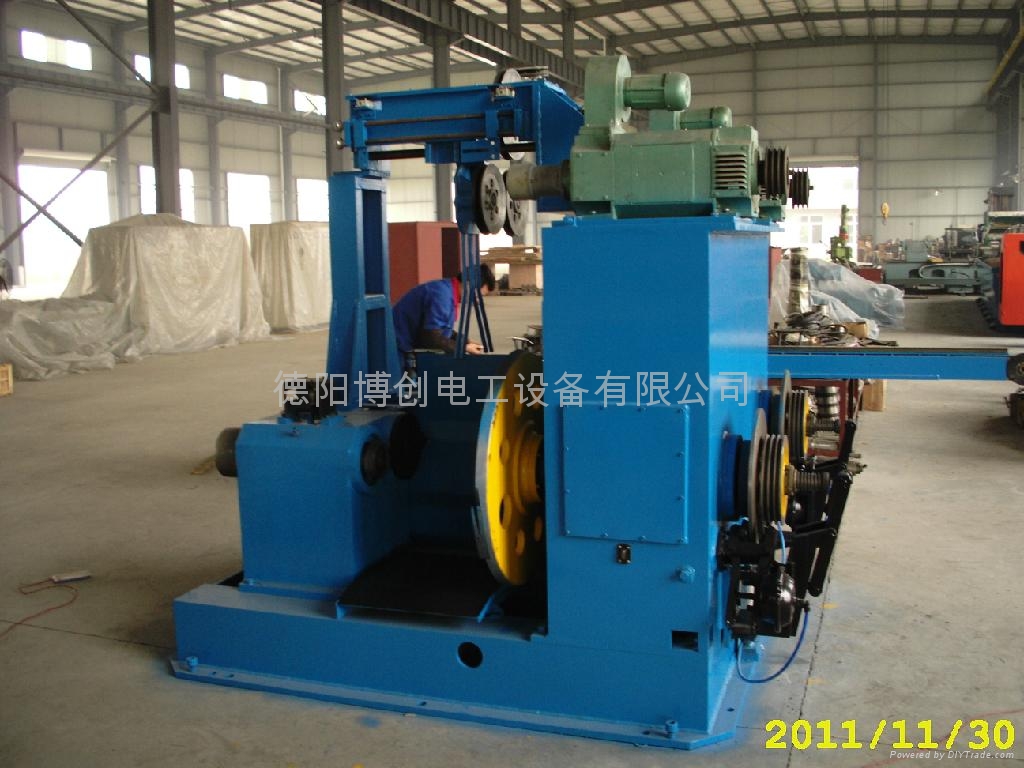